The Great Iron Pour students took off on a road trip to Loveland, Colorado early in the morning on Tuesday. The first stop the group made was Art Castings of Colorado. On our tour of the foundry, we were introduced to the procedures to make sculptures out of bronze and stainless steel. The first part of the tour was the wax mold room, where a wax version of the final sculpture is created. Other than using pure wax, the foundry also had other techniques using rubber and styrofoam. Using rubber makes the wax sculptures more stable and for big sculptures, the company send a scanned version of the wax sculpture to a different company so they can create it with styrofoam, which is lighter and easier to carry. After looking at the wax molds, we visited the next step in the procedure: Wax Chasing. There were two people in the room, fully concentrated on one single wax sculpture, making every detail of the wax sculpture into perfection. A group of students went over to one of the sculptures and talked to him about his work. He said that it took 6-8 hours on a person figure. He continued to tell the students how that even though each should be exact that each one has a bit of personality from them as they sculpt the wax figures. After the wax sculpture is ready, they needed to be invested in ceramic shell. This is the last step before it will be placed in the furnace to vacate the wax and make the casing withstand the heat of the bronze. After this, the foundry recycled their wax and the sculptures are removed from the furnace, then bronze was poured into the casing to form the actual sculpture. Afterwards, it is placed in a sand blasting device. This device helps to blast off the unnecessary parts and cleans up the metal sculpture. Coloring with a chemical process called patina is the next step before finally finishing up. This experience was very valuable to this ECS because not only it taught us what we needed to know to be successful in the Great Iron Pour ECS, but also taught us how giant bronze sculptures were made. Before lunch, we visited the Benson sculpture park.
We walked around the park and looked at many different sculptures made by different artists. While waking through the park, the different styles of each artists really enlightened us. We explored different ways we can control how we pour the iron and shape it the way we like. Also we learned how each piece can influence each other by the different response we had to each work.
After our visit with Art Castings of Colorado, we made a trip to the Benson Sculpture Garden, home to over 300 metal and stone sculptures. Here we were able to explore the park which was full of beautiful, creative, and different sculptures, in which were all made from unique materials. Afterwards, we went to Artworks Loveland, a community gallery and studio of local artists. We go to experience and examine the art creation process and creativity of the artists. Some of us talked with an artist who gave us some valuable advice for working with iron and metals, like explaining some techniques that he used when working with metals, including how he uses 3D printing to create lost wax type castings. We enjoyed the lessons learned and were given inspiration for our own sculpture projects. The gallery and studio spaces are connected to a maker-space, and we investigated the various fabrication, 3D machining, laser cutting and electronics areas.
On Friday, our ECS went on a trip to Strasbourg, CO, about 35 miles east of Denver. We visited the Uhrich Locomotive Works, a foundry known for making steam engine trains for customers all over the country. The owner, Marlin Uhrich, gave us a fantastic tour of the entire place, showing us the different moving parts that their foundry makes in house using techniques from the industrial revolution. During the tour, Mr. Uhrich showed us a large furnace from which they pour iron at an astounding rate of about 3 tons of iron per hour! We also had the awesome chance to see a live-action pour of bronze to make different castings, allowing us to get the opportunity to see and prepare for the activities we would be participating in on our own casting projects. After that, we went to a little theater on the property and watched a classic iron industry film from the 1950’s about the process of casting grey iron. For lunch, the workers fed us some delicious “Railroad Stew”, giving us some true insight into what railroad workers would eat in the olden days. I found that today was a very educational day, giving us very good insight into how we will soon pour iron. We also learned much about the science behind casting iron, such as why limestone is used as “flux”, an agent that cleans whatever metal you use from all of its impurities. Some people may think that the Iron Pour ECS is only about breaking big pieces of iron (though that’s definitely fun), melting it, and then pouring it. However, I have found that our ECS is much more than that — this ECS gives us a chance to see different businesses that use casting as well as inform us about the history and science behind casting and metallurgy.
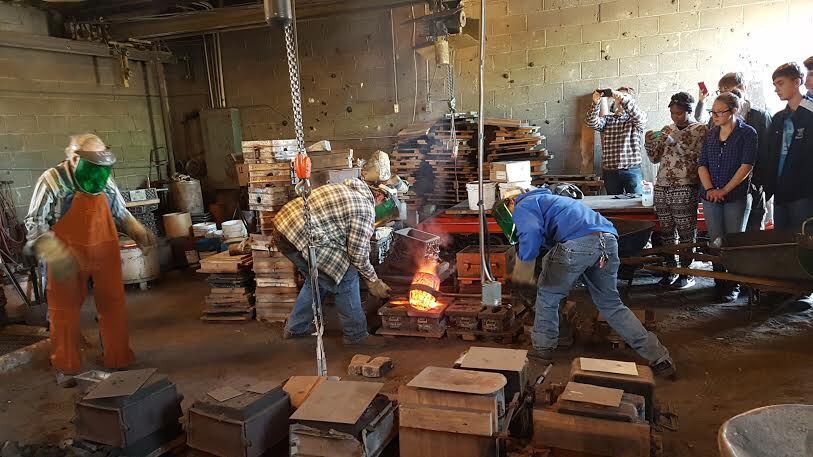
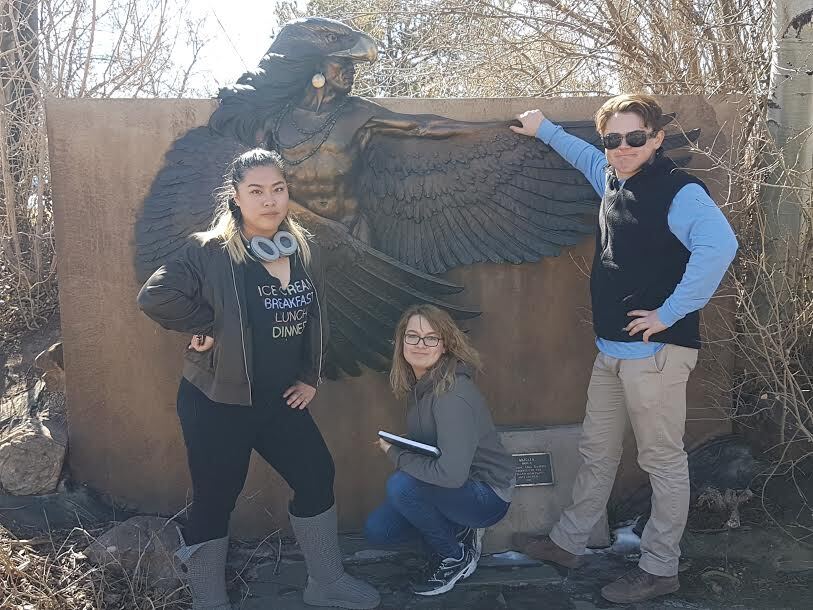
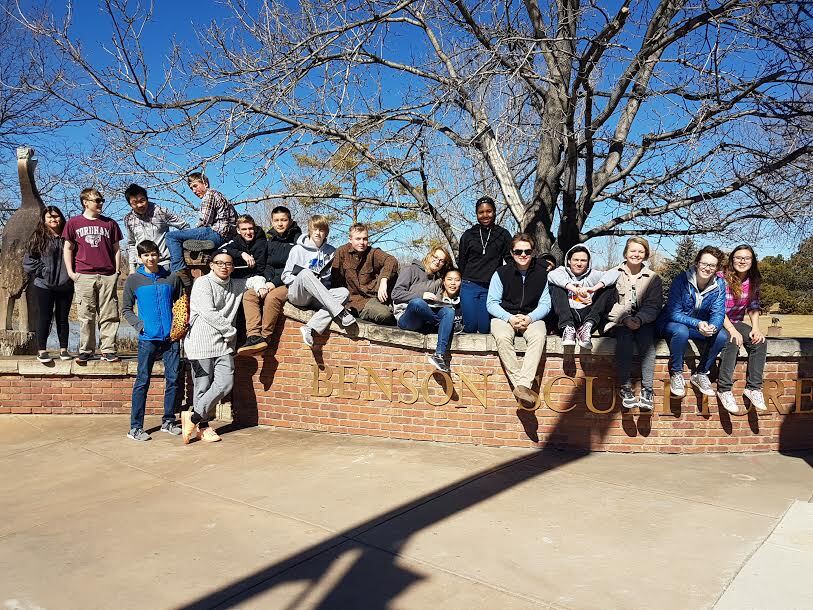