Amber W. ‘19 & Imani L. ‘19
Visit to Bliss Studio & Gallery
This past Thursday our Iron pour ECS took a trip to Bliss Studio & Gallery, established by alumna Jodie Bliss, in Monument, Colorado. She mainly focuses on hand-forged fine art Sculptures, public art, hand-forged steel, and blown glass. Jodie told us that she has been working in metal for 15 years. In those years she evolved from a jewelry fabricator into large steel sculpture fabrication and eventually into blacksmithing. Jodie can be found showing her work at art shows across the nation, and she has created custom work for private clients in Colorado, Belize, and Germany. She walked us through her gallery and studio space. I was mesmerized by the artwork, especially the ones that were mixed media, such as a steel cage with glass blown into it. As we walked around we were introduced to a wide selection of art-making processes such as bending the steel with fire, creating different textures on hot steel, and joining different objects together. The whole process of making a steel art sculpture is complex and interesting. Visiting this art gallery & studio truly opened my mind on how to use different media to create art and what all goes into the steel art industry.
Ethan H. ‘21
Preparation
The week before the pour, we had to do a lot to prepare for the pour itself, which is the culmination and the focal point of our ECS. One of the most important things on our to-do list was to break the iron from the Trianon building’s original boiler. We had to carry large hollow pieces of the boiler, weighing approximately 700 pounds, out of storage and broke it into small pieces using sledge hammers and anvils. Over the course of a week, we broke this metal into the size of about a quarter and then put into piles of 25 pounds. This was long, laborious, and tedious work. While breaking and collecting metal for a total of 60 piles weighing approximately 1,500 pounds we had to break another 60 bags of coke, a purified form of coal, each bag weighing 3 pounds. This was done with hammers and chisels and ended up taking roughly a day compared to the iron taking a whole week. One other aspect of the preparation was to prepare the molds of our artwork. A small group of 3 or 4 people began by sprueing, a technique that allows the sculpture to vent, the wax sculptures together with wax piping and a pouring funnel. This was so that when we poured the molten iron it wouldn’t create bubbles in the iron or leave small parts of the mold not filled. Then they were dipped in a ceramic slurry then covered with a layer of fused silica grit. After being given 8 or so layers of this stucco and bonding agent the molds were fired and heated up to bond the mold together to make it stronger and to melt the wax out of the molds so that they could withstand the heat of the molten iron. After setting our molds, the coke, and iron up we were nearly ready. We then set up the furnace, known as a cupola, in the courtyard. The first layer was prepared on the sand were clay was applied to the furnaces edge to seal it and was repeated for the next layer. After all of this getting finished we finally were ready for the pour on Saturday the 17th. Now, all we had to do was to show up the next day to do the pour.
Matthew P. ‘20
The Iron Pour
The time had finally come for the main event, what we had been building up to, The Great Iron Pour. We began by dividing into teams of five, with each team being four people holding the supports for the ladle. Two positions were called the pivots and held the bottom side of the support when the iron was poured, and the other two, called the pourers, lifted the other side of the support structure and controlled the rate at which the iron was poured out of the bucket holding it called the ladle. The fifth person, the slager, used a special tool to push back slag, an unwanted byproduct that was not iron so that it did not get in the molds.
Both the ladle and the slag tool had to be preheated before each pour so that the molten iron did not warp them. They would be both put on the top of the furnace where fire was shooting out, then the bucket was taken off and filled with molten iron, next the slagger would remove most of the slag from the ladle, and then finally the molten iron was poured into the molds.
Overall the iron pour was highly enjoyable and definitely worth the build up. The team work required to complete each pour really brought all the students together and in the end, no one person completed the pour, we all did. The sense of community it built was an unexpected and much-appreciated side effect of the pour and it is one of the main reasons why I personally would love to have the opportunity again.
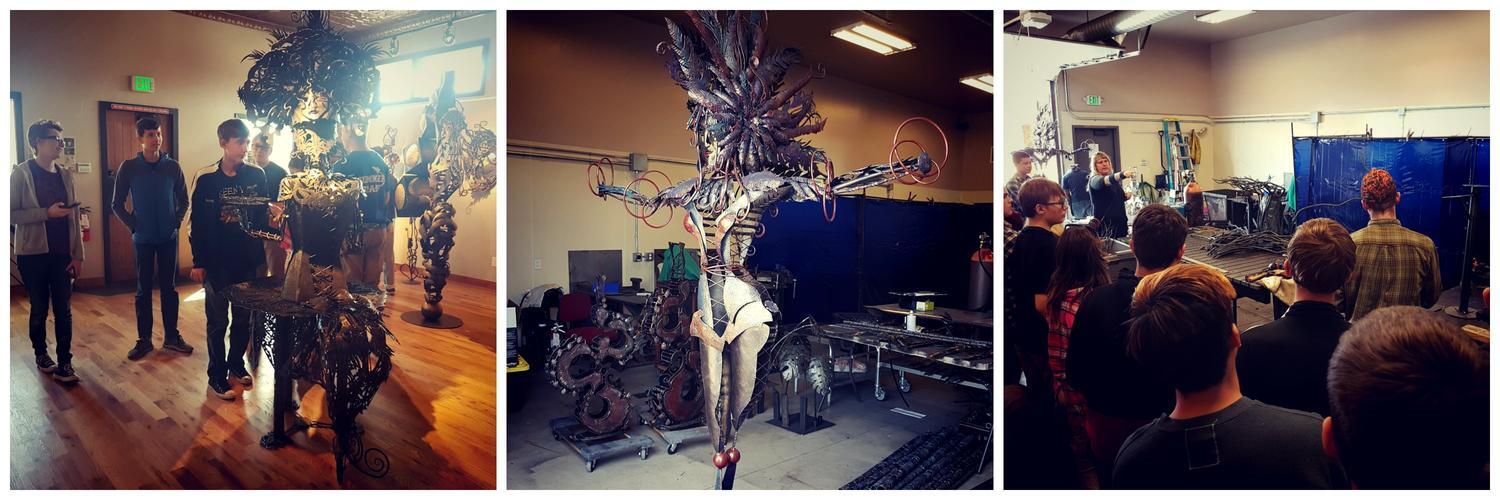
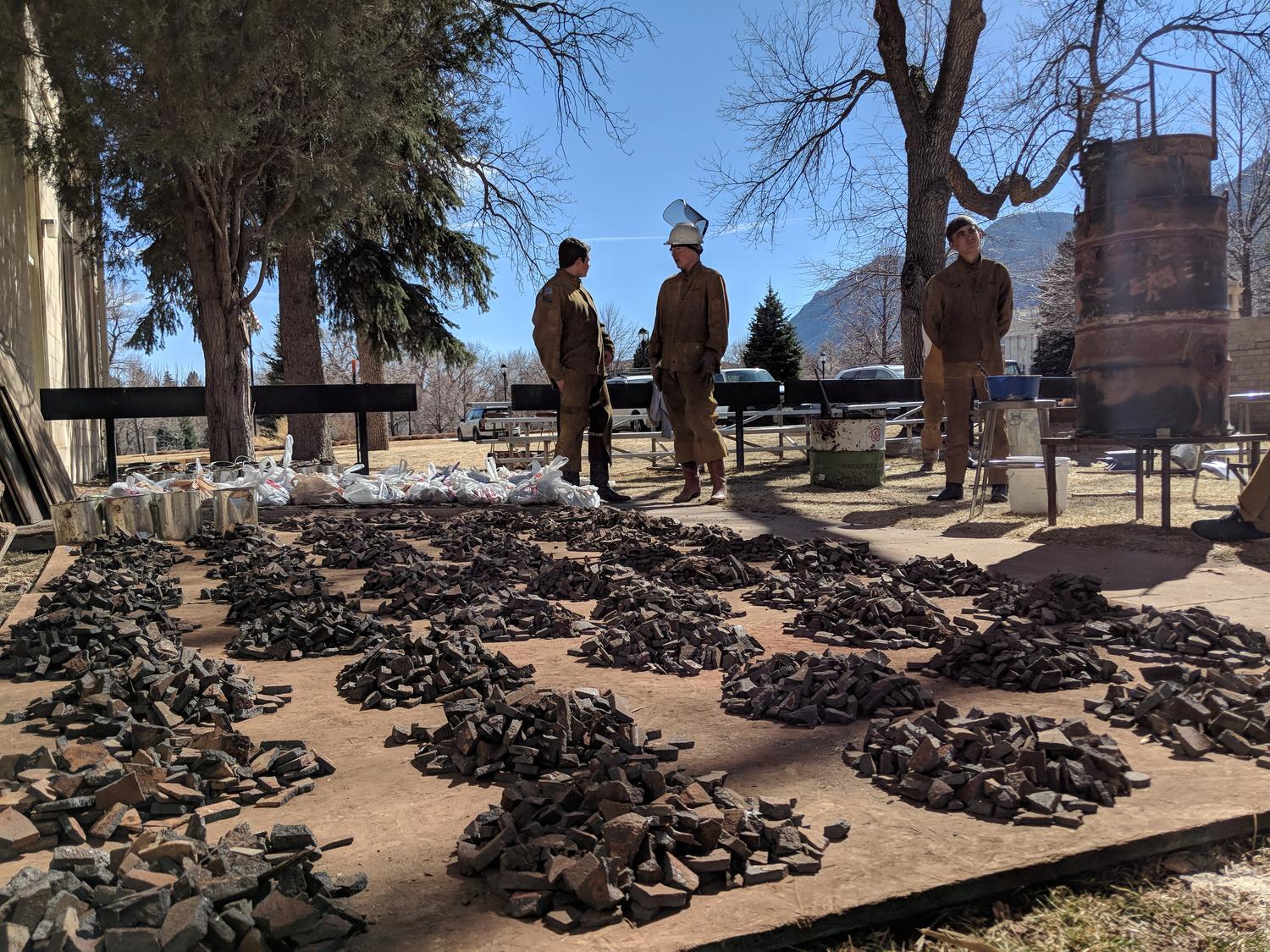
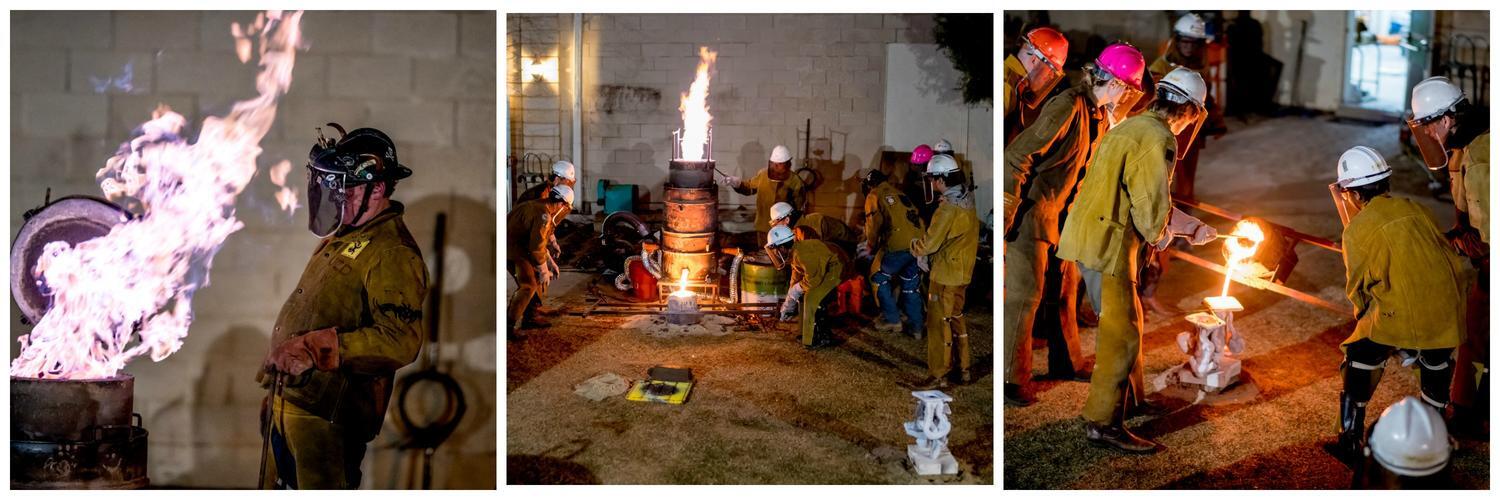